Canfor Corp. executives announced in mid June that Canfor’s 70%-owned subsidiary, Vida Group, has entered into an agreement to purchase three sawmills located in Sweden from Bergs Timber for $43 million (Can.), plus working capital…
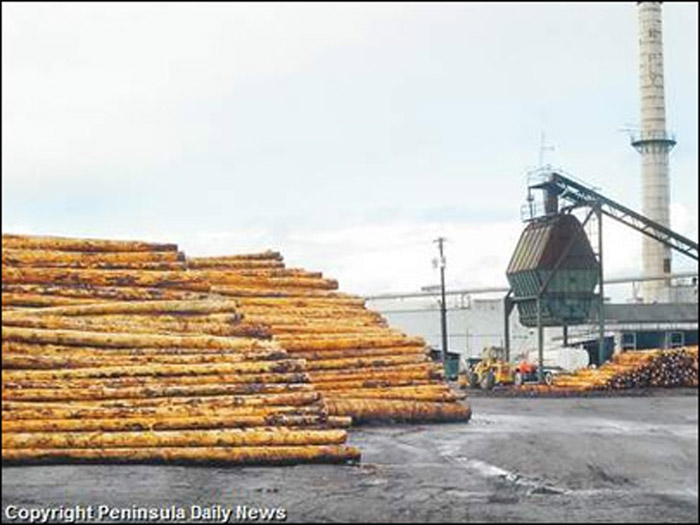
Old Plywood Mills Don’t Always Fade Away
Old Plywood Mills Don’t Always Fade Away
Article by Rich Donnell, Editor-in-Chief, Panel World January 2011
EDITOR’S NOTE: The following is an edited excerpt from the publication entitled “From Penply To K Ply,” one of a series of monographs produced by the Plywood Pioneers Assn. It complements this issue’s cover story.
They came from mill towns across western Washington and Oregon—the seasoned plywood production men who founded Peninsula Plywood Corp. in 1941. PenPly began as an idea in the minds of two Hoquiam, Wash. men, Oscar Groth and Carl Stromberg. Working together in the machine shop of the Polson Logging Company near Hoquiam, they discussed the success of worker-owned plywood mills such as Olympia Veneer. They looked throughout western Washington and western Oregon for a suitable manufacturing site “near a supply of peeler logs.” Port Angeles was one of the first locations considered.
Early in 1941, a team drawn from potential shareholders made a three-week tour of Northwest communities to promote the idea of a new mill. The team included Emory Moore, a salesman who agreed to serve as PenPly’s president during the construction phase and who later was to rise to national leadership in the plywood industry; Loren Haugen, who was to become the corporation’s chief engineer, and who in later years was to head up his own mills in Roseburg and Medford, Ore.; Carl Jacobson, who was to serve as vice president, then production superintendent, and in later years become a principal of Southern Oregon Plywood, Grants Pass, Ore.; and Herman Halvarson, who was to be the first treasurer.
On April 13, 1941, Peninsula Plywood Corporation was formally organized in Longview, Wash. The corporation was registered with the state of Washington in papers showing $500,000 capital on the basis of 350 shares of common stock at $1,000 per share and 1,500 shares of preferred stock at $100 par value per share. Each of the common shareholders was to have one vote in the organization, work at an equal wage, and receive income from a wage scale that could fluctuate according to market ups and downs.
From the beginning, PenPly called itself a “semi-cooperative.” Although 350 shares of common stock were authorized, only 285 shares were issued as there were to be only 285 jobs available at startup. The initial wage was $1.25 per hour, of which 25 cents was withheld and applied to mill capital.
The Port Angeles Evening News estimated that 75% of PenPly’s original stockholders were Scandinavian born or of Scandinavian descent. The majority of the worker owners at PenPly had extensive previous plywood manufacturing experience in Washington and Oregon.
The late Clarence Flatau recalled the huge challenge faced by the ordinary working man in raising the $1,000 needed to buy a share in 1941. Interviewed in 1971, Flatau described making an initial deposit of just $5 to treasurer Halvarson, who accepted it with obvious confidence that Flatau would soon come up with the rest of the money. He did this by selling his car and borrowing the rest.
For Flatau and many others, that hard-won investment would eventually prove to be worth far more than any of the pioneer shareholders could have imagined. A PenPly working share of $1,000 in 1941 grew to be worth $300,000 in 1971, counting job income and appreciation in share value.
Latest News
Canfor’s Vida Group Buys Sweden Mills
Indonesia To Keep Export License System
Backing off an earlier announcement that Indonesian wood products exporters would no longer need to obtain a license showing the wood’s origin and legality, Indonesia’s Ministry of Trade recently reversed itself after an outcry…
Next Xylexpo To Be Held In 2022
The Board of Cepra-Centro promozionale Acimall, orgaziners of Xylexpo, speaking through its president Lorenzo Primultini, officially canceled the 2020 show on July 6, 2020. Initially scheduled for late May in Milan, Italy, Xylexpo was first…
Find Us On Social
Newsletter
The monthly Panel World Industry Newsletter reaches over 3,000 who represent primary panel production operations.
Subscribe/Renew
Panel World is delivered six times per year to North American and international professionals, who represent primary panel production operations. Subscriptions are FREE to qualified individuals.
Advertise
Complete the online form so we can direct you to the appropriate Sales Representative. Contact us today!