Dieffenbacher Emission Control Systems
Dieffenbacher’s emission control solutions include emission measurements and dryer and press emission control systems. Emission measurements help plant operators understand which emissions are present and determine the type and amount of emissions. For example, using state-of-the-art methods, uncomplicated in-house emission measurements can be taken on stacks downstream of the dryer or the press exhaust system. This includes measuring parameters such as total organic carbon (TOC) and many different substances such as water, carbon dioxide, carbon monoxide, nitrous oxide, methane, ethane, propane, formaldehyde, methanol and other gases. Dust in the exhaust gas can also be measured using additional equipment. Subsequent correlation analyses of production parameters and emissions provide a better understanding of plant emissions.
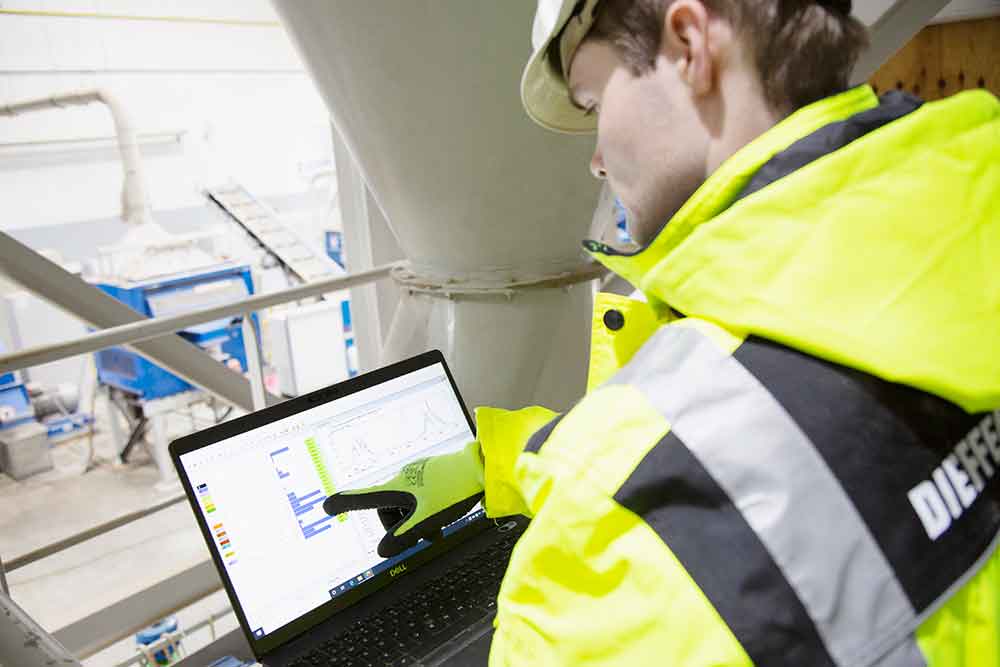
The Dryer Emission Control System cleans dryer exhaust gases using an inline scrubber in compliance with local environmental standards. The main components are the unique inline scrubber and water treatment and distribution systems. The inline scrubber efficiently separates dust particles from the gas stream. Optional auxiliary equipment captures water-soluble VOCs, notably formaldehyde. The Dryer Emission Control System is applicable for horizontal and vertical operation and costs less than an electrostatic filter. It also impresses with its low freshwater demand, reliable design for high uptime and small space requirements.
The Press Emission Control System cleans exhaust gases from the press through a washing process. Dust and condensable fractions of exhaust gases are bound to fine water droplets. These solid and liquid parts are separated in the inline scrubber. Pre-Absorber units can be supplied to reduce VOC emissions (volatile organic compounds), particularly formaldehyde. As a fluid-optimized system, the Press Emission Control System is highly energy-efficient. Like the Dryer Emission Control System, it is characterized by low freshwater demand and small space requirements.
Latest News
Kronospan Completes Simsboro Particleboard Purchase
Kronospan, a producer of wood panel products, has announced the closing of its purchase of Roseburg’s Simsboro, La., particleboard facility following the expiration of the required regulatory review period. Ownership of the plant has been transferred from Roseburg to Kronospan…
Hymmen’s Dr. Werner Pankoke Dies
Werner Pankoke, died at the age of 85 following a stroke. Born March 29, 1938 as the third child of Bielefeld, Germany dentist Dr. Wilhelm Pankoke, Werner decided not to follow in his father’s footsteps when he began his studies. Instead, he was drawn to Munich Technical University, where he pursued his grandfather Theodor Hymmen’s engineering interests—studying mechanical engineering…
Metsä Group, Sweco Sign Agreement For Design Of LVL Mill
Metsä Group and Sweco have signed an agreement for the implementation planning of the new Kerto LVL mill in Äänekoski, Finland. “We have strong confidence in Sweco’s expertise and resources from our previous collaboration projects. It is therefore natural that we continue our cooperation in this project to develop the Äänekoski mill area,” says Jaakko Anttila, Executive Vice President, Metsä Wood…
Siempelkamp Sells KüstersPress, ContiPress Technology To Sunds Fibertec
On December 12th Siempelkamp and Sunds Fibertech signed an agreement for the sale of the KüstersPress and ContiPress service business. With this transaction Sunds Fibertech will become the OEM supplier for this technology area; the transfer date will be January 3rd, 2024…
Weyerhaeuser Enhances Coastal Holdings
Weyerhaeuser Co. entered into two agreements with Forest Investment Associates to divest 69,600 acres in upstate South Carolina for $170 million, and to purchase 60,700 acres of high-quality timberlands in coastal North Carolina, South Carolina and Mississippi for $163 million…
Find Us On Social
Newsletter
The monthly Panel World Industry Newsletter reaches over 3,000 who represent primary panel production operations.
Subscribe/Renew
Panel World is delivered six times per year to North American and international professionals, who represent primary panel production operations. Subscriptions are FREE to qualified individuals.
Advertise
Complete the online form so we can direct you to the appropriate Sales Representative. Contact us today!