Georgia-Pacific Camden Plywood Invests $18 Million
It was in the late 1800s when the small community of Camden, Tex., welcomed its first forest products mill. What began as the W.T. Carter Lumber Co. is today one of Georgia-Pacific’s largest plywood operations. To ensure its longevity for years to come, Georgia-Pacific is embarking on a $18 million upgrade that will modernize the plant and help increase efficiency.
The capital improvement plan will focus on three different projects beginning with the plant’s dryer. “We’re rebuilding our dryer, which is more than 40 years old,” says George Standley, Camden Plywood Plant Manager. “The dryer is the heart and soul of plywood operations and is one of the most important stages of production. Controlling veneer’s moisture content is critical to producing a quality product.” The dryer project, supplied by Grenzenbach, is scheduled to be completed in July.
While Grenzenbach is reconditioning the dryer, the facility will also modernize its stenciling and strapping operation. Currently the mill manually stencils and straps. “This area of operation can sometimes slow down the process since an operator has to manually place a stencil on a bundle of plywood, paint it and remove the stencil. This process must be performed several times to ensure that all the required markings are captured clearly,” says Standley. The new automated strapper and stenciling system is currently being installed.
Later this summer, Camden Plywood will wrap up its capital improvement projects with the introduction of its robotic patch system. Currently patching veneer is handled by multiple workers who are stationed on the line. According to Standley, the technology will be operated by four robotic technicians who are now being trained on the system.
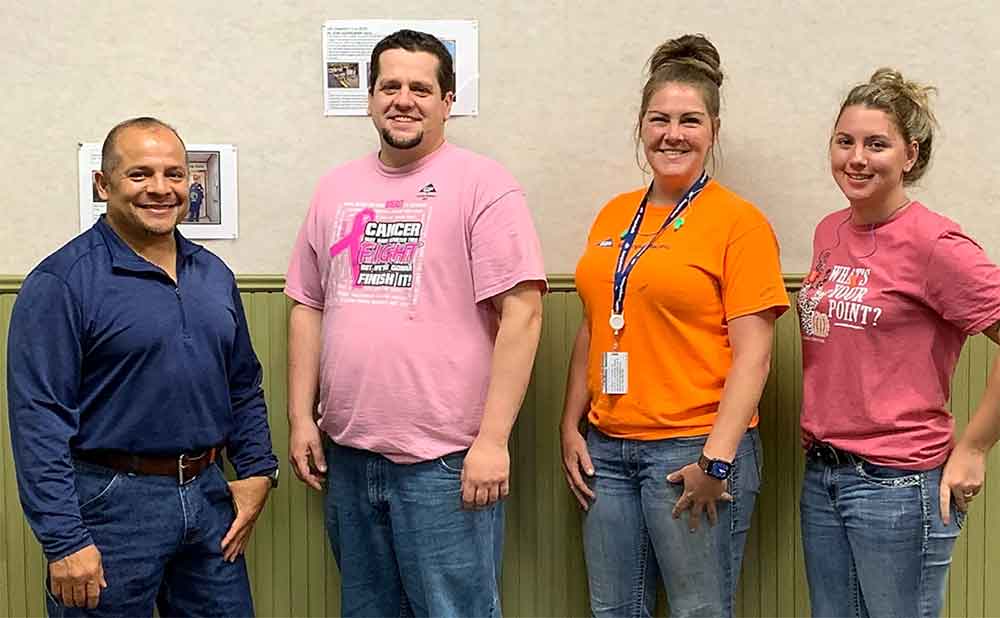
From left to right, Edgar Damian, Georgia-Pacific Precision Technician and Robotic System Trainer, and new Robotic Technicians Nathan Clark, Cristine Klenke, and Victoria Nickerson
“Camden Plywood is an example of how plants are being modernized to not only improve production, but to attract, retain and challenge industry employees,” says Standley. “Modern technology can challenge employees and give them the opportunity to grow their careers. By adding robots to our lines, it is our goal to provide more meaningful work which leads to greater job satisfaction.”
Georgia-Pacific’s Camden Plywood employs approximately 500 people and over the next few months more than 100 contractors will be onsite performing the upgrades.
RELATED ARTICLES
Latest News
Siempelkamp Expands Leadership Team
Siempelkamp Expands Leadership Team The Siempelkamp Group is realigning its Management Board to include seven members to bundle market-oriented core competencies together and integrate a modern management concept. Martin Scherrer, CEO of the Siempelkamp Group, will be...
Con-Vey Adds Sales Manager
Con-Vey, a leading provider of industrial automation and custom material handling equipment, has appointed industry veteran Jon Stults as its new sales manager. Stults, with nearly three decades of experience in the industry, will play a pivotal role in advancing Con-Vey’s sales strategies and processes…
Tolko Names New Chief Operating Officer
Brad Thorlakson, President and CEO of Tolko Industries, has announced that Pino Pucci, Vice President of Sales, Marketing and Logistics will assume a newly created interim role as Tolko’s Chief Operating Officer. “This role has been created to support our succession planning process, as Pino will eventually succeed me as President & CEO,” Thorlakson says. “Pino’s proven leadership experience, significant focus on people and culture, and his alignment with our values make him the perfect…
RoyOMartin Employees Better Themselves
The RoyOMartin University (ROM-U) program identifies emerging leaders and develops their potential to ensure that the company maintains a pipeline of leaders prepared to take the next step in their careers. Recently, Louisana-based RoyOMartin recognized Luke Briley, dry end manager, RoyOMartin-Plywood; Brett Danzy, mechanical maintenance superintendent, RoyOMartin-Plywood; Jermaine Davis, corporate purchasing coordinator, corporate office); and…
Find Us On Social
Newsletter
The monthly Panel World Industry Newsletter reaches over 3,000 who represent primary panel production operations.
Subscribe/Renew
Panel World is delivered six times per year to North American and international professionals, who represent primary panel production operations. Subscriptions are FREE to qualified individuals.
Advertise
Complete the online form so we can direct you to the appropriate Sales Representative. Contact us today!