PELICE 2022 Brought Everything From Taguchi To Board Quality Control
Article by Rich Donnell, Editor-in-Chief, Panel World September 2022
PART THREE: This is the third of a four-part series summarizing the presentations delivered during the Panel & Engineered Lumber International Conference & Expo (PELICE) held this spring and hosted by Panel World in Atlanta March 31 to April 1. The first two parts appeared in the May and July issues of Panel World, and the fourth and final selection will be in the upcoming November issue.
ATLANTA, Ga. – Terry Liles, director of raw materials, Huber Engineered Woods, dug into the application of EVOP (Evolutionary Operation) and Taguchi Design. He defined EVOP as an ongoing mode of using an operating full-scale process so that information on how to improve the process is generated from a simple experimental design while production is underway.
He noted two methodologies for conducting EVOPs: Factorial Designs, a scientific experiment that determines the influence of multiple factors on the subject, while assuming the process is consistent or under control; and Robust Product Design (or Taguchi Design), a methodology to improve the quality of a product by minimizing the effect of variation without eliminating the causes, and with minimal sensitivity to variation in uncontrollable factors or noise.
With either design approach, it’s most important to understand and state the objective for the experiment. “If you can’t define the purpose, why are you doing it?” Have a general model of the process and understand the variation; that is, the total variation is the sum of the real product variation and the measurement system variation; and the measurement system variation is the sum of the variation due to repeatability and due to reproducibility.
The sampling strategy is of utmost importance, including the number of samples and tests; and data integrity is crucial. “Am I collecting the right data to answer the questions I’m asking?”
One of the advantages of EVOP is the inclusion of many team members, Liles said, and an effective means of communication is essential such as an information board with results, statistics, deviations, graphs, etc.
He noted that Taguchi design as an EVOP is most suitable with a larger number of factors and levels, and when fewer experiments are needed; when you’re able to measure the impact of uncontrolled variables; and when there’s a targeted response objective. Whereas Factorial Design is better when the number of factors and levels is small, experiments are not time-consuming and the costs for the experiments are low, and when a combination of factors could be significant contributors to the response.
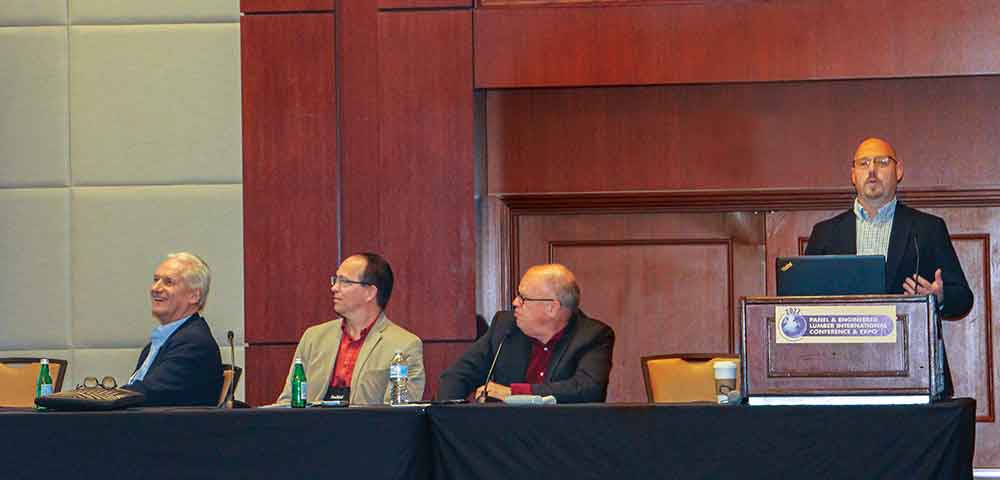
Left to right, Tim Young, Justin Price, Terry Liles and Jeff Vaughn get into experimental methodology.
Jeff Vaughn, eastern regional technical and CI manager for Roseburg, also addressed Design of Experiment Methodology as compared to traditional model of experimentation. The current state of experiments and trials is mostly the “best guess” approach and “one factor at a time” approach, Vaughn said.
The best guess approach has advantages through the technical and theoretical knowledge and practical experiences of team members, but this approach is generally not very efficient and can exclude better solutions. The one factor at a time approach is a simple, baseline approach with simple analysis, but fails to consider possible interaction between the factors and doesn’t gain enough data to deliver statistical significance.
An alternative approach is statistical design of experiments, including Taguchi, which refers to the process of planning and executing an experiment so that the proper data will be collected an analyzed through statistical methods, resulting in effective and unbiased conclusions.
QUALITY CONTROL
A series of presentations addressed Quality Control, including one by Richard Lepine, general manager with Argos Solutions. He touched on automatic grading and surface defect inspection technology, initially showing its obvious benefits (speed, defect size and location, no labor issues, verification, etc.) compared to visual inspection.
He defined new standards for TFL surface defects (such as dirt, spots, fibers, scratches, and area size) and revealed Argo’s automated detection system for printed pattern TFL, including detection of hidden defects in complicated patterns, automatic adjustment for inaccuracies in paper, stretch/shrink, rotation; special illumination; and no learning mode required; and noted the Argos use of different light angles; and finally addressed Argos’ real time monitoring and database system and reporting for categorization and statistical analysis.
Keith Mays, president of EWS North America, addressed a range of quality control products from Electronic Wood Systems GmbH, Baumer Inspection Gmbh and Monitor Plus GmbH. He hit on spark detection/extinguishment and board scanning and measurement from EWS, and the SicoScan system in collaboration with Siempelkamp, and within SicoScan the EcoScan NEO – FBD (foreign body detector) and FLY area weight measurement.
He provided detail on Baumer’s ColourBrain 4.0 optical top and bottom inspection of raw board, including a new illumination module, running through a Q-Live server environment that provides database, networking and is user-friendly. He addressed Q-Brain, which classifies the defects while QLive provides full transparency to leverage process optimization.
He also spoke in detail on Monitor Plus, a system that monitors product quality and actives alarm signals or a production stop if quality specifications are not met. It features SMART camera technology and is designed for any kind of conveying system and entails the latest data processing for its numerous product scanning and detection tasks and functions ranging from bowing to cupping, twisting, curvature, to number of drill holes in wood components, particleboard edge porosity, laminate color and glossiness, profile and contour measurement, through multiple line laser thickness measurement.
Continuing with the theme of board scanning and quality control, Michael Spurgin, sales manager North America for Limab, spoke about the different building materials that Limab’s scanning and measurement system caters to. He said Limab’s thickness measurement eliminates the effects from vibrations and bumps.
He noted several benefits with in-line measurement, from consistency to reduced downtime and increased yield; and the benefits of non-contact versus contact roller systems, including measurement on soft material like insulation to thin board to high speed and rough surfaces, while measurement starts immediately at the front edge of panels.
He pointed to multiple locations for Limab installation in a typical board processing line, including after the press, either before or after the sander (verifying that the final product is within tolerances), and with double effectiveness if measurement scanners are located both before and after the sander while using one PC; as well as a three point sander configuration including between the heads.
Jason Kovacik, sales manager with Finna Sensors, spoke on production enhancements and profitability by using IoT data-driven moisture control measurement sensors. He reviewed why IoT sensors are trending, including real-time process data, visibility of process trends and conditions, and more focused analysis. Compared to non-enabled sensors, IoT sensors enable cloud-based updates, remote diagnostics, and monitoring of sensor health and performance.
Kovacik spoke on the criteria for integrating IoT-enabled sensors into your process, including partnering with the right organization and having a strategy for adoption. More technology-specific, he focused on Finna’s OMNIR noncontact, non-destructive, real-time moisture control measurement, which features white light, near-infrared energy filtering and resonance frequency of water molecules, and with advantages built into the associated and minimized system hardware.
Kovacik talked about the company’s RF technology including an in-line meter that delivers a full moisture map of boards/pieces; and he addressed their in-line acoustic technology for strength grading.
Finna’s products can be implemented and provide value throughout the process, from incoming raw material to drying, energy production and final product quality.
AIR TREATMENT
Jaymie Deemer, President of Nestec, Inc., gave an in-depth look at dryer WESP and RTO systems, including the complexities of wood dryer emissions sometimes associated with the dryer technologies and with the particulate materials themselves. Some of these issues, as well as others, can contribute to common ESP and RTO issues and problems.
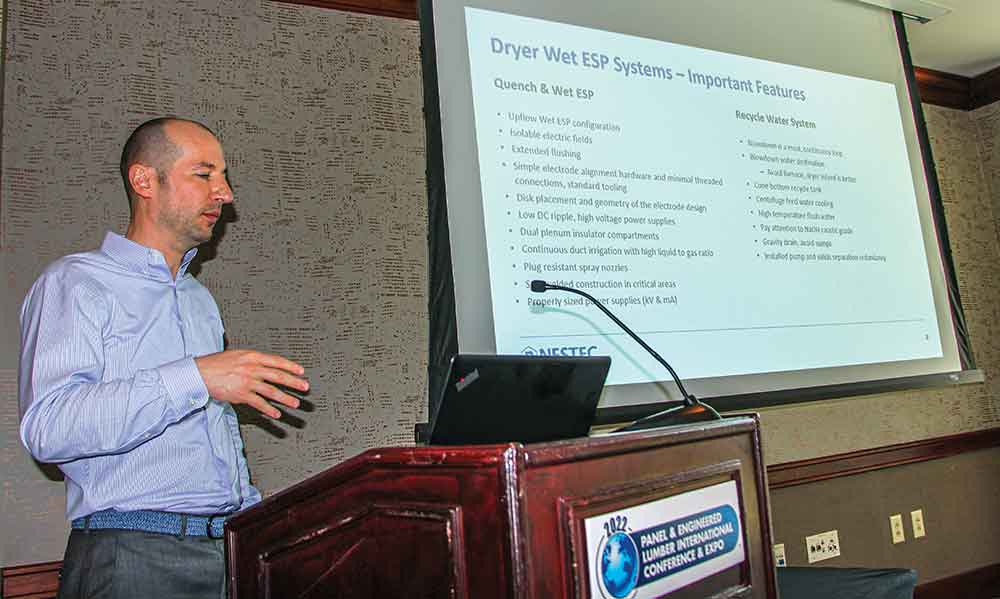
Nestec President Jaymie Deemer provides WESP and RTO dos and don’ts.
He said, “Wet ESP performance and design of critical components are key to reliable operation, and pointed to numerous such features in both WESP and RTO design, including, in the former, isolable electric fields, extended flushing, simple electrode alignment, irrigation, plug resistant spray nozzles, power supply, continuous loop blowdown, high temperature water flush, caustic grade; and in the latter, proper media, draft arrangements, multiple burners, and proper construction materials such as mastic coatings to protect the shell from condensation, and which materials to avoid such as low grade stainless steel.
Rodney Schwartz, vice president Sales & Business Development, Dürr Systems, spoke on the development and testing of new WESP design enhancements including an optimized electrode and tube design. After reviewing various factors that influence WESP performance, and issues and concerns with current designs, he said Dürr approached producers and operators to get their input on current designs. The feedback included: tubes and electrodes get dirty and are difficult to clean, potentially impacting collection performance; capital cost is too high; installation time is too long; foaming problems; mist carryover into RTOs; performance drop when flushed.
Dürr promptly set goals for a new WESP based on the feedback, including modular shipping design, better fabrication, flexible sizing, new patentable ideas, online cleaning, offline flushing.
Dürr developed a 1/6th to-scale test model and performed testing over 16 weeks with 27 separate flow tests and 55 different particulate removal tests. Testing included various configurations of electrodes, including bottom mounted discharge electrodes that proved highly effective, including the use of a High Area Trap (HAT) that showed numerous benefits.
They then built a to-scale 25,000 acfm pilot WESP that was installed at an OSB customer site in the Southern U.S. and was tested for 10 months downstream of rotary flake dryers. The new designs scored high compared to older designs on filterable particulate removal, organic condensable particulate removal, enhanced spray system cleaning and showed numerous other benefits.
The key features of the new product include maximum removal efficiencies, reliable operation, low operating costs, and significantly reduced maintenance.
Steve Jaasund, Geoenergy Products Manager for LDX Solution, addressed the benefits of RCOs for wood dryer VOC control, which is not a common practice. He noted the principle of operation for an RCO is similar to the RTO while the catalyst allowed lower combustion chamber temperature and offers significant energy savings.
He spoke on scenarios for catalyst deactivation such as poisoning, sintering and masking, but noted poisoning is not a likely problem for wood fired dryers as common poisons are not present in flue gases, alkali sintering occurs at higher tempertures than are typical for an RCO, and while masking can occur if particulate concentration is too high, he recommended ensuring that particulate loading (inlet fly ash) is low enough, upsizing the wet ESP during the initial design and/or adding a second field to the wet ESP, implementing catalyst wash out on an as-needed basis, and conducting regular catalyst performance testing.
His energy consumption chart showed significant annual savings (annual fuel cost, annual electric cost) with an RCO system compared to RTO at various gas prices, with RCO payback in a few years. The path forward, Jaasund said, is to install test blocks or thief baskets in existing RTOs operating on a wood fired dryer, and he noted existing RTOs can be catalyzed easily.
Latest News
Arauco Considers Plant In Mexico
Arauco is conducting an Environmental Impact Assessment as the first step toward evaluating the viability of a new $200 million MDF production line in Zitácuaro, Michoacán, Mexico. If the project proceeds, subject to the approval of local and state authorities, production is expected to start during 2024. It would double…
West Fraser Buys OSB Mill
An oriented strandboard plant in Allendale, SC will now have its third ownership since starting up in 2006. West Fraser Timber Co. Ltd. is purchasing the facility from Georgia-Pacific for $280 million. The Allendale facility has been idle since late 2019 when GP shut it down citing market conditions. The plant has an estimated…
USNR, WFG Sold To Equity Firm
One Equity Partners (OEP), a middle market private equity firm, announced that it has completed the previously announced acquisitions of USNR and Wood Fiber Group. OEP reports it subsequently merged the two businesses, with projected 2021 revenues greater than $500 million…
Lend Me Your Ear
Article by Rich Donnell, Editor-In-Chief, Panel World January 2022 – The staff at Panel World magazine is in full in-person-conference mode in preparation for the eighth Panel & Engineered Lumber International Conference & Expo (PELICE) to be held March 31 to April 1 at the Omni Hotel at CNN Center in Atlanta…
Idaho Producers Supply Mass Timber Arena
Industry stakeholders of all types worked to supply materials for the recently opened ICCU Basketball Arena at the University of Idaho in Moscow. The 4,000 seat facility, which opened in October 2021, incorporates several innovative mass timber elements across some of the longest spans in the country. Designers and engineers…
Pandemic Felt Bad, Profits Felt Good
Article by Rich Donnell, Editor-In-Chief, Panel World November 2021 – Given that Panel World is published six times per year, the November issue before your eyes represents the final issue of 2021. I’ve read through the six issues and pulled a few highlights of what went on in the panel world in 2021 as reported by Panel World…
Sherwin-Williams Enters Resin Game
Sherwin-Williams is acquiring Specialty Polymers, Inc., a leading manufacturer and developer primarily of water-based polymers used in architectural and industrial coatings and…
NESTEC Names Jaymie Deemer President
NESTEC, Inc. has hired Jaymie Deemer as President. Deemer brings nearly 20 years of experience in emission control technologies and nearly 25 years in the industry. He has worked with…
PELICE Adds Keynoters, Exhibitors
Organizers of the eighth Panel & Engineered Lumber International Conference & Expo (PELICE) have announced a partial list of keynote speakers for the event, which will be held Thursday-Friday, March 31 to April 1, 2022 at the Omni Hotel at CNN Center in downtown Atlanta, Georgia, USA…
Forest Service Says 4FRI Is Still Alive
Following its cancellation of the Phase 2 Request for Proposal (RFP) and bid selection in September, which caught everybody by surprise, the Forest Service “has gone back to work” on how to move forward with stewardship and treatment of the 520,000 acres that was included in Phase 2, which was part of the 4 Forests…
CalPlant I Regroups, Sale Is Possible
CalPlant I, LLC, which took 25 years to develop and build a rice straw-based medium density fiberboard plant and produce its first board late last year in Willows, Calif., has voluntarily filed for Chapter 11 bankruptcy protection and intends to conduct a court-supervised sale process…
NewLife Gains Full Production
NewLife Forest Restoration has ramped up production at its new engineered wood products plant in Bellemont, Ariz., while also increasing forest restoration work in service of its 4 Forest Restoration Initiative (4FRI) Phase 1 Forest Service stewardship contract that seeks to thin and treat more than 300,000 acres at risk of…
Labor, Materials Issues Cause Project Delays
The same labor availability issues that have plagued forest products manufacturers since the COVID pandemic began are also plaguing builders as the economy seeks to rebound. According to a survey of more than 2,000 construction companies, both hourly and salaried employees are…
There’s No Time Like The Future
Article by Rich Donnell, Editor-In-Chief, Panel World September 2021 – As I write this, several of us on the editorial staff are about to head to Atlanta, Georgia where we will be exhibiting our sawmill magazine, Timber Processing, at the Southern Forest Products Assn. lumber machinery exposition in the Georgia World…
Roseburg To Shut Down Dillard P’board
Roseburg Forest Products (RFP) announced on August 25 that it will shut down its particleboard plant in Dillard, Ore. The plant has been in operation since 1965, and will continue running as the plant prepares for shut down in the next 60 days…
Digital Platform Is Presented
Beginning September 27 exploreSiempelkamp will participate in the digital event, LIGNA.Innovation Network, organized by Deutsche Messe AG and the VDMA Woodworking Machinery Assn…
Producers Announce Personnel Changes
PotlatchDeltic Corp. has appointed Ashlee Cribb as Vice President, Wood Products. She succeeds Tom Temple, who is retiring in October after serving in this role since 2009. “We are thrilled to welcome Ashlee,” comments Eric Cremers, PotlatchDeltic…
Arboreal Plans CLT Facility In Uruguay
Equipment and technology supplier Ledinek reports it has been selected to supply a CLT line for a new venture, Arboreal, in Tacuarembó, Uruguay. In March 2021, businessman Mark Crandall from the United States and Matías Abergo, CEO of…
Martco Announces Corrigan “Two”
Martco L.L.C. (RoyOMartin) announced that its Texas subsidiary, Corrigan OSB, L.L.C., will invest $211 million and construct a stand-alone oriented strandboard (OSB) manufacturing facility near its current OSB plant located in Corrigan on U.S. Highway…
Mercer Purchases Katerra CLT Facility
Mercer International Inc., a global forest products company based in Vancouver, BC, reported it received approval from the applicable Bankruptcy Court for the purchase by its subsidiary, Blue Varsity, of the cross-laminated timber manufacturing facility in…
Find Us On Social
Newsletter
The monthly Panel World Industry Newsletter reaches over 3,000 who represent primary panel production operations.
Subscribe/Renew
Panel World is delivered six times per year to North American and international professionals, who represent primary panel production operations. Subscriptions are FREE to qualified individuals.
Advertise
Complete the online form so we can direct you to the appropriate Sales Representative. Contact us today!