PELICE 2022 Brought Everything From Taguchi To Board Quality Control
Article by Rich Donnell, Editor-in-Chief, Panel World September 2022
PART THREE: This is the third of a four-part series summarizing the presentations delivered during the Panel & Engineered Lumber International Conference & Expo (PELICE) held this spring and hosted by Panel World in Atlanta March 31 to April 1. The first two parts appeared in the May and July issues of Panel World, and the fourth and final selection will be in the upcoming November issue.
ATLANTA, Ga. – Terry Liles, director of raw materials, Huber Engineered Woods, dug into the application of EVOP (Evolutionary Operation) and Taguchi Design. He defined EVOP as an ongoing mode of using an operating full-scale process so that information on how to improve the process is generated from a simple experimental design while production is underway.
He noted two methodologies for conducting EVOPs: Factorial Designs, a scientific experiment that determines the influence of multiple factors on the subject, while assuming the process is consistent or under control; and Robust Product Design (or Taguchi Design), a methodology to improve the quality of a product by minimizing the effect of variation without eliminating the causes, and with minimal sensitivity to variation in uncontrollable factors or noise.
With either design approach, it’s most important to understand and state the objective for the experiment. “If you can’t define the purpose, why are you doing it?” Have a general model of the process and understand the variation; that is, the total variation is the sum of the real product variation and the measurement system variation; and the measurement system variation is the sum of the variation due to repeatability and due to reproducibility.
The sampling strategy is of utmost importance, including the number of samples and tests; and data integrity is crucial. “Am I collecting the right data to answer the questions I’m asking?”
One of the advantages of EVOP is the inclusion of many team members, Liles said, and an effective means of communication is essential such as an information board with results, statistics, deviations, graphs, etc.
He noted that Taguchi design as an EVOP is most suitable with a larger number of factors and levels, and when fewer experiments are needed; when you’re able to measure the impact of uncontrolled variables; and when there’s a targeted response objective. Whereas Factorial Design is better when the number of factors and levels is small, experiments are not time-consuming and the costs for the experiments are low, and when a combination of factors could be significant contributors to the response.
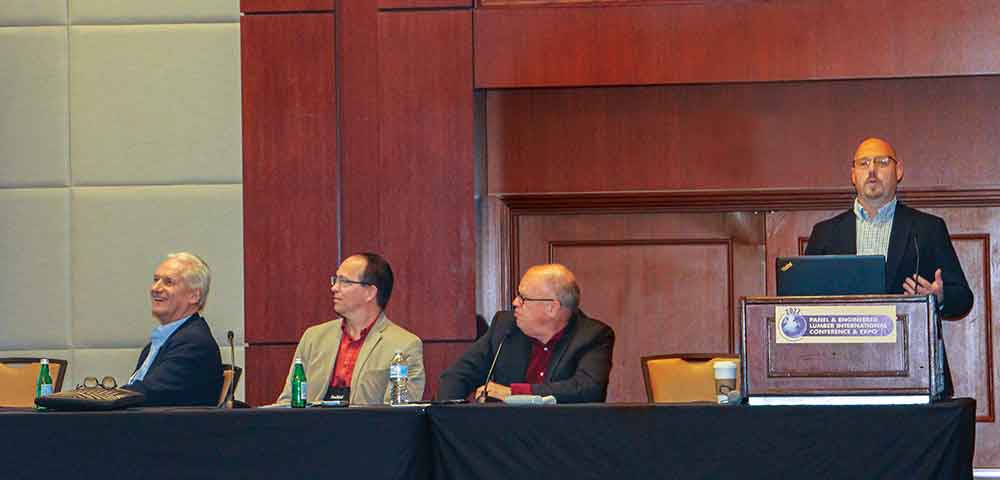
Left to right, Tim Young, Justin Price, Terry Liles and Jeff Vaughn get into experimental methodology.
Jeff Vaughn, eastern regional technical and CI manager for Roseburg, also addressed Design of Experiment Methodology as compared to traditional model of experimentation. The current state of experiments and trials is mostly the “best guess” approach and “one factor at a time” approach, Vaughn said.
The best guess approach has advantages through the technical and theoretical knowledge and practical experiences of team members, but this approach is generally not very efficient and can exclude better solutions. The one factor at a time approach is a simple, baseline approach with simple analysis, but fails to consider possible interaction between the factors and doesn’t gain enough data to deliver statistical significance.
An alternative approach is statistical design of experiments, including Taguchi, which refers to the process of planning and executing an experiment so that the proper data will be collected an analyzed through statistical methods, resulting in effective and unbiased conclusions.
QUALITY CONTROL
A series of presentations addressed Quality Control, including one by Richard Lepine, general manager with Argos Solutions. He touched on automatic grading and surface defect inspection technology, initially showing its obvious benefits (speed, defect size and location, no labor issues, verification, etc.) compared to visual inspection.
He defined new standards for TFL surface defects (such as dirt, spots, fibers, scratches, and area size) and revealed Argo’s automated detection system for printed pattern TFL, including detection of hidden defects in complicated patterns, automatic adjustment for inaccuracies in paper, stretch/shrink, rotation; special illumination; and no learning mode required; and noted the Argos use of different light angles; and finally addressed Argos’ real time monitoring and database system and reporting for categorization and statistical analysis.
Keith Mays, president of EWS North America, addressed a range of quality control products from Electronic Wood Systems GmbH, Baumer Inspection Gmbh and Monitor Plus GmbH. He hit on spark detection/extinguishment and board scanning and measurement from EWS, and the SicoScan system in collaboration with Siempelkamp, and within SicoScan the EcoScan NEO – FBD (foreign body detector) and FLY area weight measurement.
He provided detail on Baumer’s ColourBrain 4.0 optical top and bottom inspection of raw board, including a new illumination module, running through a Q-Live server environment that provides database, networking and is user-friendly. He addressed Q-Brain, which classifies the defects while QLive provides full transparency to leverage process optimization.
He also spoke in detail on Monitor Plus, a system that monitors product quality and actives alarm signals or a production stop if quality specifications are not met. It features SMART camera technology and is designed for any kind of conveying system and entails the latest data processing for its numerous product scanning and detection tasks and functions ranging from bowing to cupping, twisting, curvature, to number of drill holes in wood components, particleboard edge porosity, laminate color and glossiness, profile and contour measurement, through multiple line laser thickness measurement.
Continuing with the theme of board scanning and quality control, Michael Spurgin, sales manager North America for Limab, spoke about the different building materials that Limab’s scanning and measurement system caters to. He said Limab’s thickness measurement eliminates the effects from vibrations and bumps.
He noted several benefits with in-line measurement, from consistency to reduced downtime and increased yield; and the benefits of non-contact versus contact roller systems, including measurement on soft material like insulation to thin board to high speed and rough surfaces, while measurement starts immediately at the front edge of panels.
He pointed to multiple locations for Limab installation in a typical board processing line, including after the press, either before or after the sander (verifying that the final product is within tolerances), and with double effectiveness if measurement scanners are located both before and after the sander while using one PC; as well as a three point sander configuration including between the heads.
Jason Kovacik, sales manager with Finna Sensors, spoke on production enhancements and profitability by using IoT data-driven moisture control measurement sensors. He reviewed why IoT sensors are trending, including real-time process data, visibility of process trends and conditions, and more focused analysis. Compared to non-enabled sensors, IoT sensors enable cloud-based updates, remote diagnostics, and monitoring of sensor health and performance.
Kovacik spoke on the criteria for integrating IoT-enabled sensors into your process, including partnering with the right organization and having a strategy for adoption. More technology-specific, he focused on Finna’s OMNIR noncontact, non-destructive, real-time moisture control measurement, which features white light, near-infrared energy filtering and resonance frequency of water molecules, and with advantages built into the associated and minimized system hardware.
Kovacik talked about the company’s RF technology including an in-line meter that delivers a full moisture map of boards/pieces; and he addressed their in-line acoustic technology for strength grading.
Finna’s products can be implemented and provide value throughout the process, from incoming raw material to drying, energy production and final product quality.
AIR TREATMENT
Jaymie Deemer, President of Nestec, Inc., gave an in-depth look at dryer WESP and RTO systems, including the complexities of wood dryer emissions sometimes associated with the dryer technologies and with the particulate materials themselves. Some of these issues, as well as others, can contribute to common ESP and RTO issues and problems.
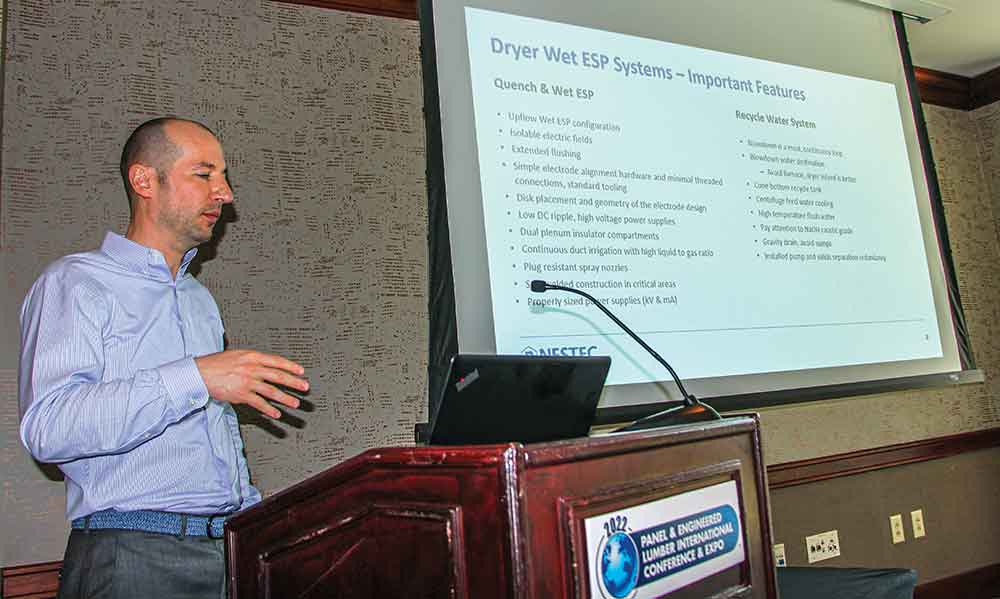
Nestec President Jaymie Deemer provides WESP and RTO dos and don’ts.
He said, “Wet ESP performance and design of critical components are key to reliable operation, and pointed to numerous such features in both WESP and RTO design, including, in the former, isolable electric fields, extended flushing, simple electrode alignment, irrigation, plug resistant spray nozzles, power supply, continuous loop blowdown, high temperature water flush, caustic grade; and in the latter, proper media, draft arrangements, multiple burners, and proper construction materials such as mastic coatings to protect the shell from condensation, and which materials to avoid such as low grade stainless steel.
Rodney Schwartz, vice president Sales & Business Development, Dürr Systems, spoke on the development and testing of new WESP design enhancements including an optimized electrode and tube design. After reviewing various factors that influence WESP performance, and issues and concerns with current designs, he said Dürr approached producers and operators to get their input on current designs. The feedback included: tubes and electrodes get dirty and are difficult to clean, potentially impacting collection performance; capital cost is too high; installation time is too long; foaming problems; mist carryover into RTOs; performance drop when flushed.
Dürr promptly set goals for a new WESP based on the feedback, including modular shipping design, better fabrication, flexible sizing, new patentable ideas, online cleaning, offline flushing.
Dürr developed a 1/6th to-scale test model and performed testing over 16 weeks with 27 separate flow tests and 55 different particulate removal tests. Testing included various configurations of electrodes, including bottom mounted discharge electrodes that proved highly effective, including the use of a High Area Trap (HAT) that showed numerous benefits.
They then built a to-scale 25,000 acfm pilot WESP that was installed at an OSB customer site in the Southern U.S. and was tested for 10 months downstream of rotary flake dryers. The new designs scored high compared to older designs on filterable particulate removal, organic condensable particulate removal, enhanced spray system cleaning and showed numerous other benefits.
The key features of the new product include maximum removal efficiencies, reliable operation, low operating costs, and significantly reduced maintenance.
Steve Jaasund, Geoenergy Products Manager for LDX Solution, addressed the benefits of RCOs for wood dryer VOC control, which is not a common practice. He noted the principle of operation for an RCO is similar to the RTO while the catalyst allowed lower combustion chamber temperature and offers significant energy savings.
He spoke on scenarios for catalyst deactivation such as poisoning, sintering and masking, but noted poisoning is not a likely problem for wood fired dryers as common poisons are not present in flue gases, alkali sintering occurs at higher tempertures than are typical for an RCO, and while masking can occur if particulate concentration is too high, he recommended ensuring that particulate loading (inlet fly ash) is low enough, upsizing the wet ESP during the initial design and/or adding a second field to the wet ESP, implementing catalyst wash out on an as-needed basis, and conducting regular catalyst performance testing.
His energy consumption chart showed significant annual savings (annual fuel cost, annual electric cost) with an RCO system compared to RTO at various gas prices, with RCO payback in a few years. The path forward, Jaasund said, is to install test blocks or thief baskets in existing RTOs operating on a wood fired dryer, and he noted existing RTOs can be catalyzed easily.
Latest News
Swanson Group Will Rebuild Oregon Plywood Mill
Swanson Group Will Rebuild Oregon Plywood MillOfficials with Swanson Group Mfg. LLC announced plans to rebuild the company’s Springfield, Ore. plywood plant after it was destroyed by fire in mid-July 2014. According to Swanson Group President and CEO Steve Swanson,...
Arauco Announces Particleboard Expansion
From: Panel World Staff Arauco is investing $30 million to expand particleboard and TFL (thermally fused laminate/melamine) capacity for its Carolina Particleboard Mill in Bennettsville, SC. The particleboard expansion, with a scheduled startup in the fourth quarter...
GP Will Upgrade Thorsby LVL
Georgia-Pacific is investing $6 million at its Thorsby, Ala. engineered lumber operations to expand production capacity of laminated veneer lumber (LVL). In a move that positions the facility for long-term success, according to the company, improvements include...
Norbord To Become Largest OSB Producer
Norbord To Become Largest OSB Producer Norbord Inc. and Ainsworth Lumber are merging and creating the largest OSB producer in the world with production capacity of 7.7 billion SF, according to the companies. The transaction entails Ainsworth shareholders...
Roseburg Has Weed Mill On Track
Roseburg Has Weed Mill On TrackRoseburg Forest Products announced a phased ramp-up of production at its Weed, Calif. veneer facility beginning October 13. The repairs to the entire mill, which was damaged by the “Boles Fire” on September 15, will likely take until the...
How Two Operations Battled Their Way Back
How Two Operations Battled Their Way Back Article by Rich Donnell, Editor-In-Chief, Panel World November 2014 We didn’t intend for this issue to have the theme of “comebacks,” but that’s how it worked out. The two main mill operation articles—on Tolko...
Swanson Transfers Springfield Workers
Swanson Transfers Springfield Workers As of late July, Swanson Group had not decided whether to rebuild its plywood mill that was destroyed by fire on the afternoon of July 17, 2014 at Springfield, Ore. CEO Steve Swanson said up to 100 employees from the...
Portland Event Continues To Emphasize Veneer-Plywood
Story by Rich Donnell, Editor-In-Chief As far as we’re concerned, the stretch run begins now for the Timber Processing & Energy Expo, which will be held October 15-17 at the Portland Exposition Center in Portland, Ore. Panel World magazine is one of the primary...
Maloney Drove Composite Board Industry Forward
Thomas M. Maloney, a pioneer and leader in the development and growth of the composite board industry, died on June 18, 2014 at his home in Pullman, Wash. He was 83. In 1967, Maloney founded the International Symposium on Particleboard & Composite Materials at...
‘He Who Is On Guard Even When Safe’
Story by Rich Donnell, Editor-In-Chief There’s a whole lot of health and safety going on in this issue. Our cover story, for example, is the Huber OSB plant in Crystal Hill, Va. The operation has implemented numerous programs and methods for the sake of its employees....
Arizona Project Moves Forward
Good Earth Power and Campbell Global (formerly The Campbell Group) officials are implementing the first phase of the ambitious 4 Forests Restoration Initiative (4FRI) across four national forests in Arizona after the original holder of the 4FRI Phase 1 contract...
TP&EE Set For October 15-17 In Portland, OR
TP&EE Set For October 15-17 In Portland, OR Hatton-Brown Expositions, LLC, an affiliate of Panel World magazine, announced in early April that the upcoming Timber Processing & Energy Expo to be held October 15-17, 2014 in Portland, Ore. is nearly sold...
Gary Raemhild Dies At 67
Gary Raemhild Dies At 67 Gary Allen Raemhild, a major figure in the development and implementation of air emissions control technology for the panel industry, died March 21 in Seattle, Wash. He was 67. Raemhild led Geoenergy International to the forefront of...
Power Of Pelice Is In The Exchange
Story by Dan Shell, Managing Editor Let’s say you operate a plywood plant and think it’s time to upgrade or replace a veneer dryer. To help in making the decision, you decide to attend the 2014 Panel & Engineered Lumber International Conference & Expo (PELICE)...
Martco Tows Dryer Into Place
Martco Tows Dryer Into PlaceIn December 2013, RoyOMartin towed into place its second fully erect 6-deck jet dryer. Just a year prior, Martco pioneered the concept of fully erecting a million pound dryer and pulling it into place as the most effective means to minimize...
Flakeboard Buys Three Mills
Flakeboard Buys Three Mills Flakeboard America Ltd., a U.S. subsidiary of Arauco, is acquiring the U.S. panel assets of SierraPine, including three composite board plants: particleboard plants at Martell and Springfield Calif. and a MDF plant at Medford, Ore....
Plywood Mills Eye Modernizations
Modernizations are a rapidly expanding trend in the plywood manufacturing business. “Companies have increasingly become more cost-aware, and therefore interested in improving their present machinery through modernizations as an alternative…
PELICE Speakers Bring Loads Of Experience
Story by Rich Donnell, Editor-in-Chief Pages 13-19 of this issue preview the upcoming Panel & Engineered Lumber International Conference & Expo, which will be held March 20-21 in Atlanta, Ga. at the Omni Hotel. This will be the fourth PELICE hosted by Panel...
BC Mills Under Dust Inspection
WorkSafeBC officers have begun another round of inspections as part of the ongoing combustible dust initiative to focus sawmills and other wood processors on keeping work sites safe. During the inspections WorkSafeBC officers examine dust accumulation; ventilation and...
The Fourth Pelice Returns To Atlanta
Story by Rich Donnell, Editor-in-Chief I have been wearing my “chairman” hat as much as my “editor” hat lately as we make preparations for the 2014 Panel & Engineered Lumber International Conference & Expo (PELICE), which will be held March 20-21 at the Omni...
Find Us On Social
Newsletter
The monthly Panel World Industry Newsletter reaches over 3,000 who represent primary panel production operations.
Subscribe/Renew
Panel World is delivered six times per year to North American and international professionals, who represent primary panel production operations. Subscriptions are FREE to qualified individuals.
Advertise
Complete the online form so we can direct you to the appropriate Sales Representative. Contact us today!