PELICE 2022 Brought Everything From Taguchi To Board Quality Control
Article by Rich Donnell, Editor-in-Chief, Panel World September 2022
PART THREE: This is the third of a four-part series summarizing the presentations delivered during the Panel & Engineered Lumber International Conference & Expo (PELICE) held this spring and hosted by Panel World in Atlanta March 31 to April 1. The first two parts appeared in the May and July issues of Panel World, and the fourth and final selection will be in the upcoming November issue.
ATLANTA, Ga. – Terry Liles, director of raw materials, Huber Engineered Woods, dug into the application of EVOP (Evolutionary Operation) and Taguchi Design. He defined EVOP as an ongoing mode of using an operating full-scale process so that information on how to improve the process is generated from a simple experimental design while production is underway.
He noted two methodologies for conducting EVOPs: Factorial Designs, a scientific experiment that determines the influence of multiple factors on the subject, while assuming the process is consistent or under control; and Robust Product Design (or Taguchi Design), a methodology to improve the quality of a product by minimizing the effect of variation without eliminating the causes, and with minimal sensitivity to variation in uncontrollable factors or noise.
With either design approach, it’s most important to understand and state the objective for the experiment. “If you can’t define the purpose, why are you doing it?” Have a general model of the process and understand the variation; that is, the total variation is the sum of the real product variation and the measurement system variation; and the measurement system variation is the sum of the variation due to repeatability and due to reproducibility.
The sampling strategy is of utmost importance, including the number of samples and tests; and data integrity is crucial. “Am I collecting the right data to answer the questions I’m asking?”
One of the advantages of EVOP is the inclusion of many team members, Liles said, and an effective means of communication is essential such as an information board with results, statistics, deviations, graphs, etc.
He noted that Taguchi design as an EVOP is most suitable with a larger number of factors and levels, and when fewer experiments are needed; when you’re able to measure the impact of uncontrolled variables; and when there’s a targeted response objective. Whereas Factorial Design is better when the number of factors and levels is small, experiments are not time-consuming and the costs for the experiments are low, and when a combination of factors could be significant contributors to the response.
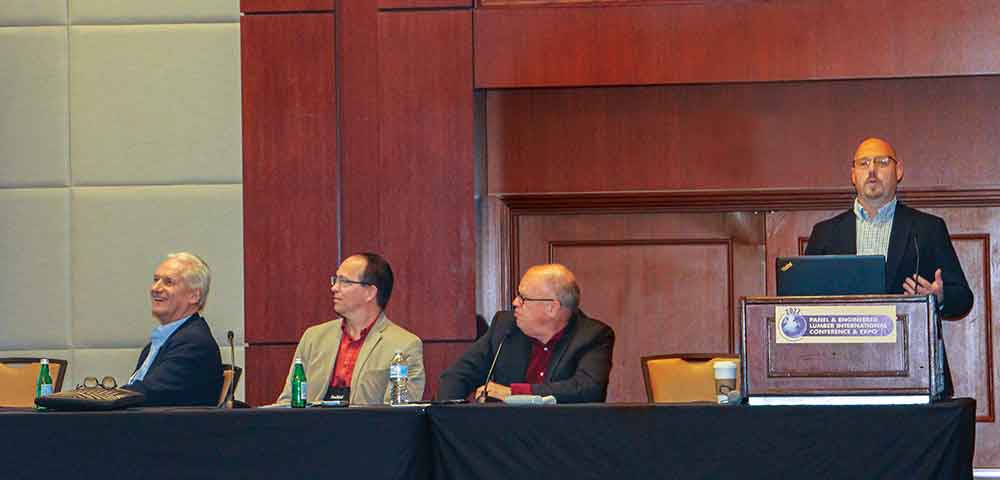
Left to right, Tim Young, Justin Price, Terry Liles and Jeff Vaughn get into experimental methodology.
Jeff Vaughn, eastern regional technical and CI manager for Roseburg, also addressed Design of Experiment Methodology as compared to traditional model of experimentation. The current state of experiments and trials is mostly the “best guess” approach and “one factor at a time” approach, Vaughn said.
The best guess approach has advantages through the technical and theoretical knowledge and practical experiences of team members, but this approach is generally not very efficient and can exclude better solutions. The one factor at a time approach is a simple, baseline approach with simple analysis, but fails to consider possible interaction between the factors and doesn’t gain enough data to deliver statistical significance.
An alternative approach is statistical design of experiments, including Taguchi, which refers to the process of planning and executing an experiment so that the proper data will be collected an analyzed through statistical methods, resulting in effective and unbiased conclusions.
QUALITY CONTROL
A series of presentations addressed Quality Control, including one by Richard Lepine, general manager with Argos Solutions. He touched on automatic grading and surface defect inspection technology, initially showing its obvious benefits (speed, defect size and location, no labor issues, verification, etc.) compared to visual inspection.
He defined new standards for TFL surface defects (such as dirt, spots, fibers, scratches, and area size) and revealed Argo’s automated detection system for printed pattern TFL, including detection of hidden defects in complicated patterns, automatic adjustment for inaccuracies in paper, stretch/shrink, rotation; special illumination; and no learning mode required; and noted the Argos use of different light angles; and finally addressed Argos’ real time monitoring and database system and reporting for categorization and statistical analysis.
Keith Mays, president of EWS North America, addressed a range of quality control products from Electronic Wood Systems GmbH, Baumer Inspection Gmbh and Monitor Plus GmbH. He hit on spark detection/extinguishment and board scanning and measurement from EWS, and the SicoScan system in collaboration with Siempelkamp, and within SicoScan the EcoScan NEO – FBD (foreign body detector) and FLY area weight measurement.
He provided detail on Baumer’s ColourBrain 4.0 optical top and bottom inspection of raw board, including a new illumination module, running through a Q-Live server environment that provides database, networking and is user-friendly. He addressed Q-Brain, which classifies the defects while QLive provides full transparency to leverage process optimization.
He also spoke in detail on Monitor Plus, a system that monitors product quality and actives alarm signals or a production stop if quality specifications are not met. It features SMART camera technology and is designed for any kind of conveying system and entails the latest data processing for its numerous product scanning and detection tasks and functions ranging from bowing to cupping, twisting, curvature, to number of drill holes in wood components, particleboard edge porosity, laminate color and glossiness, profile and contour measurement, through multiple line laser thickness measurement.
Continuing with the theme of board scanning and quality control, Michael Spurgin, sales manager North America for Limab, spoke about the different building materials that Limab’s scanning and measurement system caters to. He said Limab’s thickness measurement eliminates the effects from vibrations and bumps.
He noted several benefits with in-line measurement, from consistency to reduced downtime and increased yield; and the benefits of non-contact versus contact roller systems, including measurement on soft material like insulation to thin board to high speed and rough surfaces, while measurement starts immediately at the front edge of panels.
He pointed to multiple locations for Limab installation in a typical board processing line, including after the press, either before or after the sander (verifying that the final product is within tolerances), and with double effectiveness if measurement scanners are located both before and after the sander while using one PC; as well as a three point sander configuration including between the heads.
Jason Kovacik, sales manager with Finna Sensors, spoke on production enhancements and profitability by using IoT data-driven moisture control measurement sensors. He reviewed why IoT sensors are trending, including real-time process data, visibility of process trends and conditions, and more focused analysis. Compared to non-enabled sensors, IoT sensors enable cloud-based updates, remote diagnostics, and monitoring of sensor health and performance.
Kovacik spoke on the criteria for integrating IoT-enabled sensors into your process, including partnering with the right organization and having a strategy for adoption. More technology-specific, he focused on Finna’s OMNIR noncontact, non-destructive, real-time moisture control measurement, which features white light, near-infrared energy filtering and resonance frequency of water molecules, and with advantages built into the associated and minimized system hardware.
Kovacik talked about the company’s RF technology including an in-line meter that delivers a full moisture map of boards/pieces; and he addressed their in-line acoustic technology for strength grading.
Finna’s products can be implemented and provide value throughout the process, from incoming raw material to drying, energy production and final product quality.
AIR TREATMENT
Jaymie Deemer, President of Nestec, Inc., gave an in-depth look at dryer WESP and RTO systems, including the complexities of wood dryer emissions sometimes associated with the dryer technologies and with the particulate materials themselves. Some of these issues, as well as others, can contribute to common ESP and RTO issues and problems.
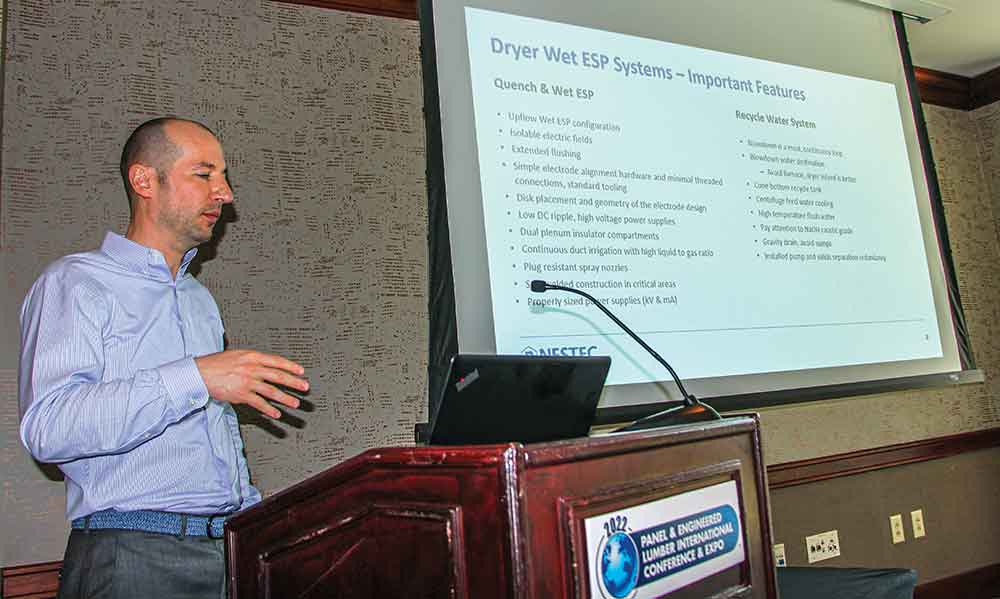
Nestec President Jaymie Deemer provides WESP and RTO dos and don’ts.
He said, “Wet ESP performance and design of critical components are key to reliable operation, and pointed to numerous such features in both WESP and RTO design, including, in the former, isolable electric fields, extended flushing, simple electrode alignment, irrigation, plug resistant spray nozzles, power supply, continuous loop blowdown, high temperature water flush, caustic grade; and in the latter, proper media, draft arrangements, multiple burners, and proper construction materials such as mastic coatings to protect the shell from condensation, and which materials to avoid such as low grade stainless steel.
Rodney Schwartz, vice president Sales & Business Development, Dürr Systems, spoke on the development and testing of new WESP design enhancements including an optimized electrode and tube design. After reviewing various factors that influence WESP performance, and issues and concerns with current designs, he said Dürr approached producers and operators to get their input on current designs. The feedback included: tubes and electrodes get dirty and are difficult to clean, potentially impacting collection performance; capital cost is too high; installation time is too long; foaming problems; mist carryover into RTOs; performance drop when flushed.
Dürr promptly set goals for a new WESP based on the feedback, including modular shipping design, better fabrication, flexible sizing, new patentable ideas, online cleaning, offline flushing.
Dürr developed a 1/6th to-scale test model and performed testing over 16 weeks with 27 separate flow tests and 55 different particulate removal tests. Testing included various configurations of electrodes, including bottom mounted discharge electrodes that proved highly effective, including the use of a High Area Trap (HAT) that showed numerous benefits.
They then built a to-scale 25,000 acfm pilot WESP that was installed at an OSB customer site in the Southern U.S. and was tested for 10 months downstream of rotary flake dryers. The new designs scored high compared to older designs on filterable particulate removal, organic condensable particulate removal, enhanced spray system cleaning and showed numerous other benefits.
The key features of the new product include maximum removal efficiencies, reliable operation, low operating costs, and significantly reduced maintenance.
Steve Jaasund, Geoenergy Products Manager for LDX Solution, addressed the benefits of RCOs for wood dryer VOC control, which is not a common practice. He noted the principle of operation for an RCO is similar to the RTO while the catalyst allowed lower combustion chamber temperature and offers significant energy savings.
He spoke on scenarios for catalyst deactivation such as poisoning, sintering and masking, but noted poisoning is not a likely problem for wood fired dryers as common poisons are not present in flue gases, alkali sintering occurs at higher tempertures than are typical for an RCO, and while masking can occur if particulate concentration is too high, he recommended ensuring that particulate loading (inlet fly ash) is low enough, upsizing the wet ESP during the initial design and/or adding a second field to the wet ESP, implementing catalyst wash out on an as-needed basis, and conducting regular catalyst performance testing.
His energy consumption chart showed significant annual savings (annual fuel cost, annual electric cost) with an RCO system compared to RTO at various gas prices, with RCO payback in a few years. The path forward, Jaasund said, is to install test blocks or thief baskets in existing RTOs operating on a wood fired dryer, and he noted existing RTOs can be catalyzed easily.
Latest News
Forest Products Industry Says Goodbye To Walter
Walter Jarck, whose career in the forest products industry spanned 65 years and ranged from logging machinery to engineered wood products, died January 3, surrounded by his children, in North Wilkesboro, NC. He was 92.
PELICE 2024 Will Cover Higher Level Focus On Markets & Technologies
The ninth Panel & Engineered Lumber International Conference & Expo (PELICE) will feature 38 speakers, while nearly 100 exhibitor sponsors will fill the Grand Ballroom North of the Omni Atlanta Hotel at Centennial Park in downtown Atlanta, Ga. USA.
Oregon Truckers File Suit Against State
Rob Freres, president of Oregon-based Freres Engineered Wood, a manufacturer of lumber, veneer, plywood and mass timber, has thrown in his support for a lawsuit filed by the Oregon Trucking Assn. and three Oregon-based trucking companies against the state of Oregon for overcharging truckers under the weight-mile tax.
Hasslacher Enters North America
Austria-based Hasslacher group is acquiring a stake in Element5, a mass timber producer specializing in the design, manufacture and assembly of modern engineered timber buildings. Based near Toronto, Can., Element5 employs more than 100 and produces cross-laminated timber and glued laminated timber for the North American market.
Endowment Welcomes New Board Members
U.S. Endowment for Forestry and Communities announces that Fritz Mason, Paul Hossain and Anna Torma were elected as new directors at the organization’s fall board meeting. “Drawing upon diverse backgrounds, they each bring a distinctive perspective and unique vision. We look forward to collaborating with them to further the mission of the Endowment,” comments Pete Madden, President and CEO of the Endowment.
FPIC At Louisiana Tech Receives Donation
Martin Sustainable Resources LLC of Alexandria, La. has donated $1 million to Louisiana Tech as a leadership gift toward construction of the University’s new Forest Products Innovation Center (FPIC), with the assurance of another $1 million to be presented by this June. The Center will be on South Campus and provide space for a transdisciplinary approach to solving the challenges…
Kadant Completes Key Knife Acquisition
Kadant Inc. has completed its previously announced acquisition of Key Knife, Inc. and some of its affiliates for approximately $156 million in cash, subject to certain customary adjustments. The acquisition was financed primarily through borrowings under Kadant’s revolving credit facility. Key Knife, a global supplier of engineered knife systems for custom chipping, planing, and flaking solutions for wood product industries, is headquartered in Tualatin, Ore. with…
PELICE 2024 Continues To Light Up Scoreboard With New Presentations
Organizers of the ninth Panel & Engineered Lumber International Conference & Expo announced that attendee registration is open for the event, which will be held March 14-15, 2024 at the Omni Atlanta Hotel at Centennial Park in downtown Atlanta, Georgia— the same location as the previous eight PELICE events…
Kronospan Completes Simsboro Particleboard Purchase
Kronospan, a producer of wood panel products, has announced the closing of its purchase of Roseburg’s Simsboro, La., particleboard facility following the expiration of the required regulatory review period. Ownership of the plant has been transferred from Roseburg to Kronospan…
Hymmen’s Dr. Werner Pankoke Dies
Werner Pankoke, died at the age of 85 following a stroke. Born March 29, 1938 as the third child of Bielefeld, Germany dentist Dr. Wilhelm Pankoke, Werner decided not to follow in his father’s footsteps when he began his studies. Instead, he was drawn to Munich Technical University, where he pursued his grandfather Theodor Hymmen’s engineering interests—studying mechanical engineering…
Metsä Group, Sweco Sign Agreement For Design Of LVL Mill
Metsä Group and Sweco have signed an agreement for the implementation planning of the new Kerto LVL mill in Äänekoski, Finland. “We have strong confidence in Sweco’s expertise and resources from our previous collaboration projects. It is therefore natural that we continue our cooperation in this project to develop the Äänekoski mill area,” says Jaakko Anttila, Executive Vice President, Metsä Wood…
Siempelkamp Sells KüstersPress, ContiPress Technology To Sunds Fibertec
On December 12th Siempelkamp and Sunds Fibertech signed an agreement for the sale of the KüstersPress and ContiPress service business. With this transaction Sunds Fibertech will become the OEM supplier for this technology area; the transfer date will be January 3rd, 2024…
Weyerhaeuser Enhances Coastal Holdings
Weyerhaeuser Co. entered into two agreements with Forest Investment Associates to divest 69,600 acres in upstate South Carolina for $170 million, and to purchase 60,700 acres of high-quality timberlands in coastal North Carolina, South Carolina and Mississippi for $163 million…
Boise Cascade Curtails Chapman Sawmill
Boise Cascade announced an indefinite curtailment of its lumber production in Chapman, Ala. The curtailment will affect 80 positions. The plywood operations at the Chapman location are not part of the curtailment. Worker Adjustment and Retraining Notification (WARN) Act notification was provided to impacted employees and specifies that operations will cease on January 28, 2024…
RoyOMartin Hosts 100 Year Celebration
On November 10 RoyOMartin celebrated the founding of Roy O. Martin Lumber Co., which was legally organized and incorporated in Alexandria, La. in 1923. Led by Indiana native Roy O. Martin, Sr., the company was started after the entrepreneur’s purchase of an older sawmill and began without a single acre of land…
Swiss Krono France Facility Upgrades Recycling
Swiss Krono S.A.S. based in Sully-sur-Loire, France and the French subsidiary of the Swiss Krono Group, strongly emphasizes the environmental aspects of its activities a key initiative of that commitment is increasing the use of recycled…
Raute Receives 93 Million Euros Order
Raute Corp. has signed a contract worth 93 million Euros with Metsä Wood, part of Metsä Group, for the technology delivery of a new Kerto laminated veneer lumber (LVL) mill in Äänekoski, Finland. This order, the…
Georgia-Pacific Mass Timber Event With Warnock
Georgia-Pacific, along with partners The Georgia Forestry Foundation and Jamestown LP, met with state and local leadership to discuss how prioritizing and utilizing sustainable structural…
PELICE Releases Technical Session Information
In addition to announced keynotes, PELICE continues to add speakers and presentations for the numerous technical sessions on tap. The full PELICE agenda is expected to be announced later this month…
PELICE 2024 Adds Two More Keynotes
Panel & Engineered Lumber International Conference & Expo (PELICE), scheduled for next March 14-15 in Atlanta, continues to add speakers to it lineup. The event, which is hosted by Panel World magazine and Georgia Research Institute, will be held for the ninth time at the Omni Hotel in downtown Atlanta…
Find Us On Social
Newsletter
The monthly Panel World Industry Newsletter reaches over 3,000 who represent primary panel production operations.
Subscribe/Renew
Panel World is delivered six times per year to North American and international professionals, who represent primary panel production operations. Subscriptions are FREE to qualified individuals.
Advertise
Complete the online form so we can direct you to the appropriate Sales Representative. Contact us today!