Roseburg Makes Major Decision
Roseburg Forest Products, which announced in April a $700 million investment over the next four years to expand operations in southern Oregon, including a $450 million MDF plant in Dillard, Ore., has selected Siempelkamp as the primary supplier of the MDF plant, including a 10 ft. x 42.1 m ContiRoll continuous press.
The companies noted that in 1969 Siempelkamp supplied Roseburg Lumber with its very first composite panel press line.
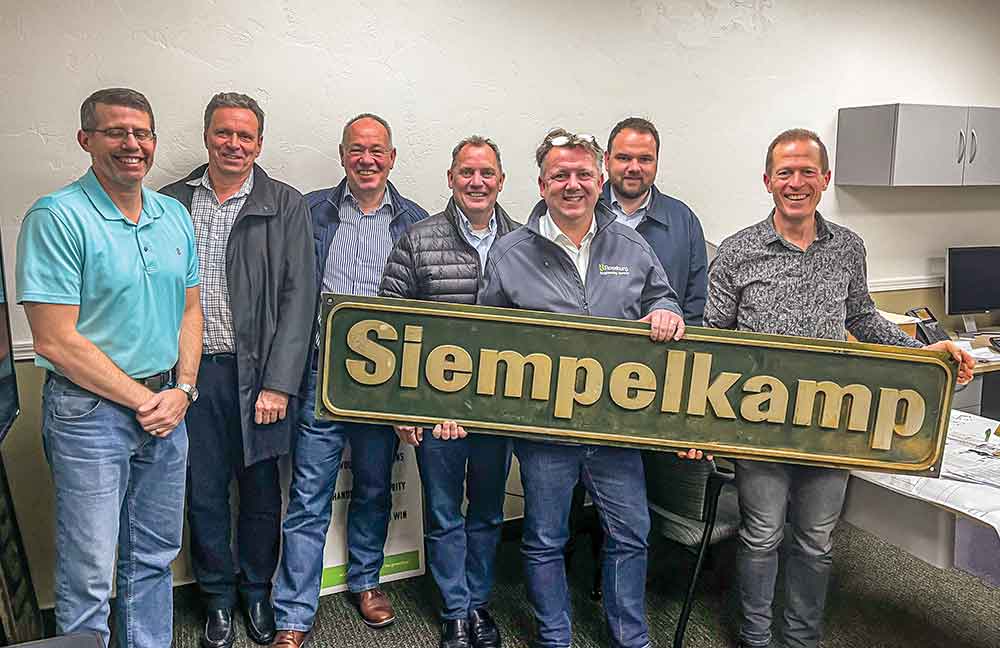
Of historic proportions. Standing with the sign from the first Siempelkamp press at Roseburg from 1969, left to right: Steve Tavernier, Director of Sourcing at Roseburg Forest Products; Joachim Meier, Executive Vice President at Siempelkamp LP; Gottfried Bluthardt, Sales Engineer at Büttner; Dirk Koltze, President at Siempelkamp LP; Ulrich Kaiser, Head of Sales Wood Division at Siempelkamp; Michael Jensen, Sales Engineer Wood Div. at Siempelkamp; Jim Salchenberg, Director of Engineering/Construction, Automation & Robotics at Roseburg Forest Products.
Roseburg’s Oregon investment, which also includes a component manufacturing center at Dillard, and upgrades to existing plants in Douglas and Coos counties, is considered to be the largest known manufacturing investment in rural Oregon and one of the largest private capital investments in the state’s history.
According to Senior Vice President of Operations, Jake Elston, “Effective manufacturing in today’s globally competitive environment requires efficient and automated equipment as well as new skills, analytical tools and work methodologies to optimize production capacity and the work environment. We are excited to be working side by side with Siempelkamp on making these things come together for a long and successful future at the new plant.”
Siempelkamp is supplying the heart of the new MDF plant. The scope of supply includes a Büttner dryer line, sifter, the forming and press line, cooling and stacking line as well as the intermediate storage and the associated automation of the machine technology. The planning of the plant by Sicoplan is also included. Also integrated is a glue saving system for MDF, which through atomization technology is said to reduce glue consumption by up to 15% while enhancing panel quality.
A EcoScan NEO measuring system will also be used, which features high resolution analysis of basis weight distribution and foreign tramp material detection directly after the prepress. Via the adaptive forming system developed by Siempelkamp, it provides a closed control loop for best and permanent forming accuracy without human intervention.
The production process is expected to use up to 100% sawdust as raw material. “Here we score with our flexible press infeed, a very precise hydraulic system for thin boards, the EcoScan NEO concept, and the adaptive MDF forming system—all decisive reasons for Roseburg Forest Products to cooperate with us again,” comments Ulrich Kaiser, Head of Sales Wood Div. at Siempelkamp.
Fifty-four years ago it was Dr. Dieter Siempelkamp, Managing Director in the third Siempelkamp generation, who sold Roseburg the first operating system for composite panels. The companies noted they are united not only by the drive to push innovations but also by the commitment to long-standing loyalty and “handshake integrity,” core values of Roseburg Forest Products and Siempelkamp alike.
Speaking of the massive investment, Roseburg President and CEO Grady Mulberry adds, “Roseburg is embracing advanced manufacturing and leveraging new technology and methods to make our current products and develop new ones, with the goal of ensuring we remain competitive in the global market. I want to thank our partners at the Governor’s office and Douglas and Coos counties for helping make this historic investment possible.”
Dillard MDF will use wood residuals from Roseburg’s local mills as well as other regional mill suppliers to manufacture standard MDF panels as well as thin high density fiberboard (HDF), often used in cabinetry, doors, and other applications. The plant will produce panels with a thickness range from 2 mm to 28 mm.
“HDF is a new product for Roseburg that meets growing customer demand for domestically manufactured panels of increasing thinness and strength,” Mulbery says.
Dillard Components will convert specialty MDF panels manufactured at Roseburg’s MDF plant in Medford, Ore., into Armorite Trim, a finished exterior trim product for residential and shed use. This is an innovative, new product currently unavailable within the industry or market, according to Roseburg, which will invest roughly $50 million in this plant.
Roseburg currently owns and operates three MDF plants in North America. The company anticipates that both new plants will begin operations in 2025, and will employ approximately 120 once completed.
The remaining $200 million of the investment will go toward improvements and significant upgrades at the plywood plant in Riddle, Ore., including two new lathe lines and a new hardwood plywood line; and a new dryer at the plywood plant in Coquille, Ore.
In June 2022, Roseburg revealed that it was exploring the feasibility of locating an additional MDF plant or other residual-based operation within its Western operating footprint. That study, combined with a years-long strategic assessment of company operations across the state, resulted in the decision to make this investment in southern Oregon, where the company was founded in 1936.
Latest News
Egger Plans Third TFL Line
Egger Wood Products will invest $20 million for an additional thermally fused laminate (TFL) production line at the company’s sole U.S. location in Lexington, NC. The company’s Supervisory Board announced the investment, part of completion for Phase I work at the site, after visiting the U.S. plant for its…
Peak Renewables Hires Scott Bax
Peak Renewables Ltd., an emerging, innovative, opportunity-driven company focused on growing the forest economy with sustainably sourced and renewable energy products, is pleased to announce that Scott Bax has been appointed as Chief Executive Officer, effective December 20, 2021...
Build Back Better Awards Oregon Group
Oregon Mass Timber Coalition was named by the Economic Development Administration (EDA) as a finalist in the $1 billion Build Back Better Regional Challenge. The coalition was awarded $500,000 to create a strategy for a Mass Timber Modular Manufacturing Facility at Marine Terminal 2 in Portland…
Wolf-Gerd Dieffenbacher Turns 70
Wolf-Gerd Dieffenbacher celebrated his seventieth birthday on December 20, 2021. Until his withdrawal from the day-to-day business on July 1, 2019, the entrepreneur was active for more than 40 years in the Eppingen-based family business Dieffenbacher GMBH Maschinen- und Anlagenbau, which he led as CEO…
American Securities Acquires Hexion
Hexion Holdings Corp. has entered into an agreement to be acquired by affiliates of American Securities LLC. The transaction is expected to close in the first half of 2022, following and conditioned upon the closing of the company’s previously announced sale of its epoxy business to Westlake Chemical Corp…
Con-Vey Launches New Web Site
Roseburg, Ore.-based Con-Vey has launched a new website in collaboration with another local Roseburg company, Anvil Northwest. The nine-month project was started with the intent to update the company’s look and promote its services. The result was a beautifully designed site with a paring down of the number…
Arauco Considers Plant In Mexico
Arauco is conducting an Environmental Impact Assessment as the first step toward evaluating the viability of a new $200 million MDF production line in Zitácuaro, Michoacán, Mexico. If the project proceeds, subject to the approval of local and state authorities, production is expected to start during 2024. It would double…
West Fraser Buys OSB Mill
An oriented strandboard plant in Allendale, SC will now have its third ownership since starting up in 2006. West Fraser Timber Co. Ltd. is purchasing the facility from Georgia-Pacific for $280 million. The Allendale facility has been idle since late 2019 when GP shut it down citing market conditions. The plant has an estimated…
USNR, WFG Sold To Equity Firm
One Equity Partners (OEP), a middle market private equity firm, announced that it has completed the previously announced acquisitions of USNR and Wood Fiber Group. OEP reports it subsequently merged the two businesses, with projected 2021 revenues greater than $500 million…
Lend Me Your Ear
Article by Rich Donnell, Editor-In-Chief, Panel World January 2022 – The staff at Panel World magazine is in full in-person-conference mode in preparation for the eighth Panel & Engineered Lumber International Conference & Expo (PELICE) to be held March 31 to April 1 at the Omni Hotel at CNN Center in Atlanta…
Find Us On Social
Newsletter
The monthly Panel World Industry Newsletter reaches over 3,000 who represent primary panel production operations.
Subscribe/Renew
Panel World is delivered six times per year to North American and international professionals, who represent primary panel production operations. Subscriptions are FREE to qualified individuals.
Advertise
Complete the online form so we can direct you to the appropriate Sales Representative. Contact us today!